What does FW mean in ELECTRONICS
FW stands for Filament Wound. It is a method of composite manufacturing that is used to produce parts that are strong and rigid. This process starts by winding either pre-impregnated or dry fibers around an object such as metal, plastic or ceramic core material, which forms the desired shape and structure of the part. After the fibers are wound in the desired configuration, the part is cured in an oven allowing the resin to harden and bind the fibers together to reinforce the part and ensure overall structural integrity.
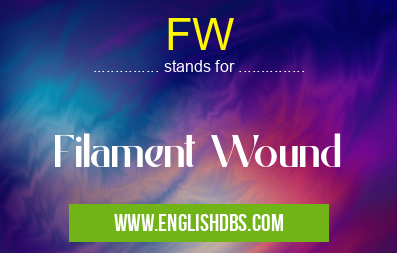
FW meaning in Electronics in Academic & Science
FW mostly used in an acronym Electronics in Category Academic & Science that means Filament Wound
Shorthand: FW,
Full Form: Filament Wound
For more information of "Filament Wound", see the section below.
What Does FW Mean?
Advantages of Utilizing FW Technology
The primary advantage of filament wound technology over other manufacturing methods is its ability to create shapes that require continuous winding paths with exact angles and orientations. This ensures that all parts produced have consistent properties throughout their entire form factor which makes them ideal for use in demanding applications where precision matters most such as aerospace components or defense systems. In addition, filament wound technology requires little labor since it is mostly automated, meaning less time spent producing parts while still achieving superior product quality.
Applications Where FW Is Used
Filament wound technology has many industrial applications across many industries including aerospace, defense, automotive, industrial equipment and medical devices due to its ability to create precise parts with strong physical characteristics even under harsh conditions like extreme temperatures or pressure changes. It is particularly useful for satellite structures, launch vehicle components, engine parts (turbine blades), gun barrels as well as fuel cells and implantable device housings due to their necessity for extreme rigidity.
Essential Questions and Answers on Filament Wound in "SCIENCE»ELECTRONICS"
What is Filament Wound?
Filament winding is a fabrication technique used to produce cylindrical items such as pressure vessels and pipes. This process involves the application of continuous filaments of fiber-reinforced resin onto a rotating mandrel. The fibers are wound in layers, with the angle and orientation in each layer determined by a computer-controlled machine. The fibers are impregnated with resin to form composite parts with superior strength and stiffness.
What materials can be used for Filament Wound construction?
Filament winding is used to construct parts from a variety of materials, including glass fibers, carbon fibers, Kevlar®, Vectran™, nylon, polyester, PEEK™ (polyetheretherketone) thermoplastic elastomers and more.
What types of products can be made using Filament Wound?
Products that can be constructed using filament winding include tanks and vessels for chemical or pharmaceutical processing; fuel storage tanks; piping systems; offshore oil drilling equipment; end fittings for aircraft wings; rocket casings; boat hulls; commercial pool slides; fire suppression equipment; structural components for aircraft landing gear; microfluidic devices and many more.
How accurate is Filament Winding?
Filament winding is capable of producing highly accurate products with a relative tolerance of 0.01 inches or better — often close to zero errors if precision machining processes are also employed. In addition, because the process is controlled digitally via software programing, repeatability across multiple parts is guaranteed.
What are the benefits of using filament winding?
The major advantages that filament winding offers include speed and efficiency — parts can be rapidly produced on automated machines with minimal human intervention required — reduced labor costs through automation, excellent weight-to-strength ratio achieved through precise fiber placement and an ability to easily customize any part’s design geometry due to computer control over the entire process. Additionally, there are no raised edges or tool marks that would otherwise need post-production finishing work.
What type of product finish can be achieved through Filament Winding?
Depending on the material used in construction different finishes can be obtained through filament winding such as glossy surfaces (e.g., glass reinforced plastics), matt surfaces (e.g., carbon reinforced thermoplastics), smooth longitudinal seams (e.g., tubing) or highly contoured structures (e.g., helicopter blades).
Is filament winding cost effective compared to other manufacturing methods?
Yes — when compared to other fabrication techniques such as compression molding or hand lay-up methodologies which both require extra costs associated with labor hours and disposal fees for waste material, filament winding offers considerable cost savings due its automation capabilities and minimized production time per unit part produced.
Are there any limitations when using Filament Winding technologies?
There are some limitations when constructing complex geometries such as deep recesses because the unfilled space between overlapping layers may cause weak spots in the final part which could result in failure during use or testing stages — extra measures must therefore taken into account when designing such components . Additionally it’s advisable not to use this method for certain types of applications that could demand extremely light weight materials as they may not be appropriately suited for this particular fabrication method.
Is it possible to employ 3D printing alongside filament winding technologies?
: Yes — one approach might involve 3D printing initial prototypes using a low cost plastic material before running two batches simultaneously — one batch using conventional filaments wrapped around a mandrel while another batch uses 3D printed components embedded into the same mold prior to curing stage thus allowing mixing both traditional methods alongside additive manufacturing processes in order to reduce time frame needed until production starts at full scale.
FW also stands for: |
|
All stands for FW |