What does SCARP mean in FDA
The Supplier Corrective Action Report (SCARP) is a document that is used to identify and track problems that arise in supplier relationships. It can be used to gather information, document findings, and propose solutions needed to address issues. The purpose of the SCARP is to ensure suppliers meet agreed-upon performance standards. With its use, supply chain professionals are better equipped to resolve potential issues with their suppliers before they become major disruptions or problems.
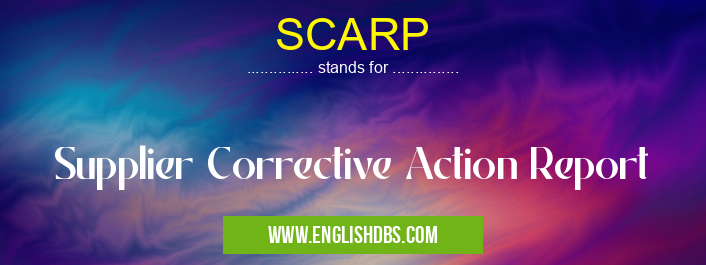
SCARP meaning in FDA in Governmental
SCARP mostly used in an acronym FDA in Category Governmental that means Supplier Corrective Action Report
Shorthand: SCARP,
Full Form: Supplier Corrective Action Report
For more information of "Supplier Corrective Action Report", see the section below.
» Governmental » FDA
What Is Supplier Corrective Action Reports
A SCARP outlines an issue or problem within a supplier relationship, and then identifies the corrective action needed. It contains information regarding the specifics about the quality defect, processes involved in the incident, timeline for completion of corrections suggested by the supplier, financial implications of failure or success on both sides of the agreement, and a timetable for follow-up evaluations by both parties. This is all done with a specific focus on preventing future incidents from happening again. It also serves as documentation for review at any future time if any disputes arise between supplier and customer. By gathering this data into one convenient document, it allows both parties to more easily identify areas where improvement is needed more quickly and efficiently compared to traditional methods such as emails or manual reviews.
Essential Questions and Answers on Supplier Corrective Action Report in "GOVERNMENTAL»FDA"
What is a SCARP?
A Supplier Corrective Action Report (SCARP) is a document that captures and describes actions taken to address issues identified in supplier corrective action requests (SCARs). The goal of a SCARP is to ensure supplier conformance to requirements and help improve performance.
What elements should be included in a SCARP?
A SCARP should include the following elements: an overview of the issue, details of any corrective action taken, evidence that the corrective action was effective, follow-up activities taken or planned, and information about lessons learned.
Who needs to review and approve a SCARP?
Generally speaking, the person or persons responsible for the management of supplier performance should review and approve a SCARP. This could include quality assurance personnel, procurement personnel, engineering personnel, etc.
How often should SCARPs be reviewed?
It is important that suppliers are monitored regularly to ensure they are performing up to standards so it is recommended that all active/open SCARPs should be reviewed at least quarterly by responsible personnel.
What actions are taken when a supplier fails to meet expectations set out in their SCARA?
Depending on the severity of failure and other factors such as their history with your organization, appropriate corrective actions may include issuing warning letters or terminating contracts with applicable suppliers.
How are potential performance issues identified?
Potential performance issues can be identified by tracking delivery times and quality results from suppliers as well as monitoring incidents reported by customers or internal users. In addition, conducting periodic audits can provide insight into potential issues that may exist with suppliers' processes.
When should suppliers receive feedback on their performance from my organization?
Feedback on suppliers' performance should ideally be provided regularly; it's best practice for both organizations involved to understand how their relationship is progressing over time. Quarterly reviews are recommended for those actively supplying goods or services at this time. Additionally, feedback for completed projects or sales transactions can also help provide additional context into specific supplier performance issues if there have been any.
What types of corrective actions might need to be taken against suppliers who fail to perform according to specified requirements?
Corrective actions are tailored based on each situation but some common types of corrective actions include providing additional training resources or materials, launching improvement plans with specific objectives & deadlines set out upfront and requiring re-submission of product samples with improved characteristics compared against what was previously submitted before final approval can be granted.
Final Words:
Overall, using Supplier Corrective Action Reports helps ensure that customers get what they need from suppliers while also providing an easily accessible system to track progress in meeting goals. All stakeholders are held accountable when following these reports which ensures that expectations are met and potential issues are addressed quickly before they cause significant delays in production or service delivery. Not only does this help maintain reliability among parties involved but also strengthens relationships between customers and suppliers over time by creating workflows that expect quality outcomes every time.