What does QCI mean in UNCLASSIFIED
QCI stands for Quality Control Inspection. It is a systematic and independent examination of a product, service, or process to ensure that it meets specified requirements. The purpose of QCI is to identify and correct any defects or non-conformities that may impact the quality of the final product or service.
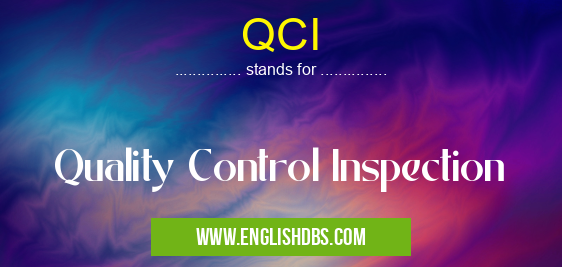
QCI meaning in Unclassified in Miscellaneous
QCI mostly used in an acronym Unclassified in Category Miscellaneous that means Quality Control Inspection
Shorthand: QCI,
Full Form: Quality Control Inspection
For more information of "Quality Control Inspection", see the section below.
Components of QCI
QCI involves various components that contribute to its effectiveness:
- Inspection Plan: Outlines the specific requirements, acceptance criteria, and inspection methods to be followed.
- Sampling: Determines the subset of the population to be inspected, ensuring a representative evaluation.
- Inspection Methods: Involves visual inspection, measurement, testing, or other techniques to assess the quality of the item.
- Non-Conformance Reporting: Documents any deviations from the specified requirements, allowing for corrective action.
- Corrective Action: Identifies the root cause of non-conformities and implements measures to prevent their recurrence.
Benefits of QCI
Implementing QCI offers numerous benefits for organizations:
- Improved Product Quality: Ensures that products meet customer expectations and industry standards.
- Reduced Defects: Identifies and eliminates defects early on, reducing the likelihood of costly rework or customer complaints.
- Enhanced Customer Satisfaction: Provides assurance that products and services are of high quality, leading to increased customer loyalty.
- Increased Productivity: By detecting and correcting defects promptly, QCI minimizes production downtime and improves overall efficiency.
- Regulatory Compliance: Meets regulatory requirements and standards, preventing legal and financial penalties.
Implementation
Effective implementation of QCI requires careful planning and execution:
- Establish Clear Standards: Define specific quality requirements and acceptance criteria for the product or service.
- Develop an Inspection Plan: Outline the inspection methods, frequency, and responsibilities of the inspection team.
- Train Inspectors: Ensure inspectors are adequately trained to perform inspections accurately and consistently.
- Implement Corrective Action: Establish a process for identifying and addressing non-conformities to prevent their recurrence.
- Continual Improvement: Regularly evaluate the QCI process and make necessary adjustments to enhance its effectiveness.
Essential Questions and Answers on Quality Control Inspection in "MISCELLANEOUS»UNFILED"
What is Quality Control Inspection (QCI)?
QCI is a process that involves examining products or services to ensure they meet specified quality standards. It aims to prevent defective or non-conforming items from reaching customers, thereby safeguarding product reputation and customer satisfaction.
What are the benefits of QCI?
QCI offers numerous benefits, including:
- Reduced production costs by identifying and eliminating defects during production.
- Improved product quality, leading to increased customer satisfaction and loyalty.
- Enhanced brand reputation by ensuring that only high-quality products or services are delivered to customers.
- Reduced risk of product recalls or legal issues stemming from defective or non-compliant products.
- Streamlined production processes by identifying and addressing quality issues early on.
Who performs QCI?
QCI can be performed by various individuals or teams within an organization, depending on the size and nature of the business. Common roles involved in QCI include:
- Quality control inspectors
- Quality assurance managers
- Production supervisors
- Engineers
- Product designers
What are the different types of QCI methods?
There are several QCI methods, including:
- Statistical sampling: Inspecting a representative sample of products or services to assess overall quality.
- 100% inspection: Inspecting every single product or service.
- Automated inspection: Using machines or software to perform automated quality checks.
- Visual inspection: Manually inspecting products or services for defects or non-conformances.
- Dimensional inspection: Measuring products or components to ensure they meet specifications.
What are the key elements of an effective QCI program?
An effective QCI program typically involves the following elements:
- Clearly defined quality standards and specifications.
- Trained and experienced inspectors.
- Standardized inspection procedures.
- Proper documentation and record-keeping.
- Feedback mechanisms to continuously improve the QCI process.
Final Words: QCI plays a vital role in ensuring the quality of products, services, and processes. By identifying and correcting defects, it significantly enhances customer satisfaction, reduces costs, and improves overall business performance. Implementing a comprehensive QCI program is essential for organizations seeking to deliver high-quality offerings and achieve long-term success.
QCI also stands for: |
|
All stands for QCI |